As the world gets more digitally connected, a new group of people demands more variety, convenience, and businesses that employ more ecologically friendly business methods. This has had a significant impact on sectors, particularly in the food and beverage sector. It’s no longer enough for food and beverage plants to be smarter, more efficient, and cost-effective; they must also be more sustainable.
To be truly green, businesses must consider every aspect of their operations, from ensuring that the manufacturing site respects the local ecosystem to decreasing energy and water waste during production. It also entails collaborating with environmentally conscious vendors. This calls for the concept of sustainable factories. How can you create a factory that is more efficient in every way? A factory that contributes to a more efficient supply chain, allowing you to manufacture more high-quality goods faster while lowering your environmental impact? The answer to this is sustainable factories.
The Concept of Sustainable Factories
The manufacturing site itself is an excellent location to start. Because, to be sustainable, you must also consider the environment around you, which involves ensuring that the building has the least potential impact. This includes decreasing pollution during construction or repair and ensuring that the project protects and preserves the environment and natural resources around it. It also entails including a stormwater drainage system in your plans to increase on-site infiltration and decrease the impact on natural water systems.
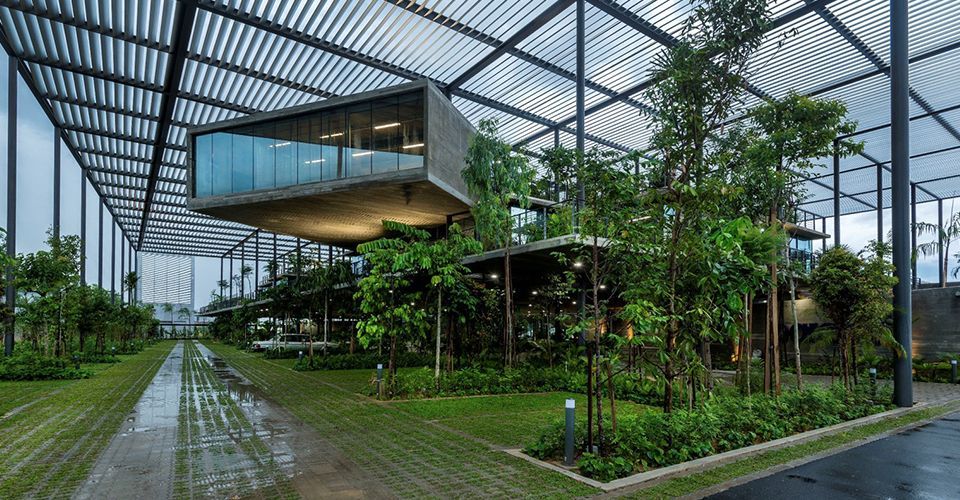
The growing collaboration between renewable energy and industry also plays a crucial role. As a result, with industrial heating and cooling accounting for a significant portion of global energy consumption, employing the IIoT to create more energy-efficient systems can play a significant role in assisting businesses in transitioning to a more sustainable production model. For some manufacturers, this has meant heating their facilities with electricity supplied from renewable energy sources. This is known as “renewable power-to-heat,” It compels firms to install electric boilers in their factories, such as those that can heat water for space heating. Biomass – which can be made from wood, straw, manure, or even algae – has many potentials for sustainable energy sources. However, acquiring biomass that is both sustainably generated and low-cost can be difficult for enterprises. Replanting trees is one technique to reduce the environmental impact of biomass, which emits CO2 when burned.
Manufacturers can make changes on a more immediate level if they look outside of renewable energy sources. If we look at food and beverage manufacturers, this may imply only working with suppliers who are also environmentally conscious. It could also entail using environmentally friendly materials to build factories, revising recipes to eliminate unsustainable ingredients, and implementing environmentally friendly cleaning techniques, among other things.
Implementing Strategies to Ensure Sustainable Factories
The term “resource optimisation” refers to the process of ensuring that labour and non-labour resources, including labour, plants and equipment, materials, and suppliers, are all aligned. So, what’s the best course of action? It could be as easy as strategically positioning machinery and other equipment on the factory floor. For example, as anybody who works in manufacturing knows, it makes sense to store goods near a loading dock while preparing them for delivery, reducing the number of trips personnel must make to load items into trucks. Simply put, you want employees to have quick access to their workstations. Thus, the architecture of a factory has a significant impact on your supply chain.
Another thing to consider while developing an atmosphere that is suitable for sustainable factories is air quality. This could entail using non-volatile organic compound cleaning products and paints or reducing chemical emissions during manufacturing – perhaps by incorporating a wet scrubber into your plans. Selecting a low-maintenance flooring system that does not require polishing, stripping, or waxing also helps. The amount of chemicals needed in day-to-day cleaning and maintenance is reduced even more.
You might want to make it a point to be more conscious of the vendors with whom you work. Because it makes sense to be aware of the raw materials you use if you assure low pollutants during manufacturing and have a well-thought-out and efficient factory floor. A pre-qualification check is one technique to verify suppliers. Is their environmental management system certified, and what is their track record for following green standards and policies? You may employ digital technology to understand your machinery better and improve the way you use it by analysing data. This can help industry workers operate more effectively while also extending the life of their equipment. You might also utilise digital tools to track and trace products, assisting in the early detection of problems and reducing waste.
Creating Greener and Sustainable Factories
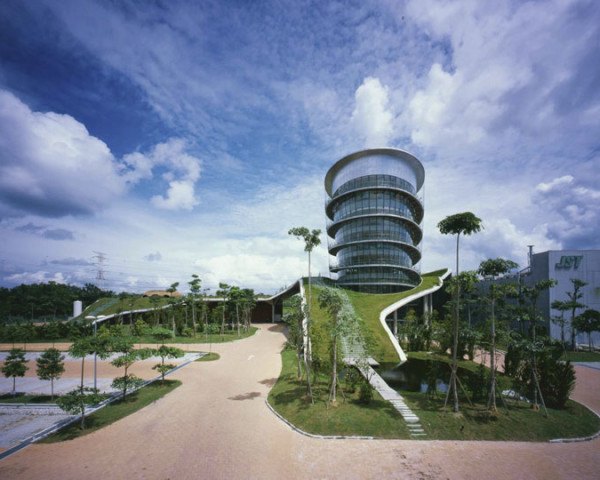
Industry accounted for 37 per cent of worldwide final energy use in 2018, up 0.9 per cent yearly since 2010. As a result, producers might use an energy management team for auditing any systems that use water, air, gas, electricity, or steam to fulfil expanding consumer expectations while also obtaining energy efficiency. In addition, optimal peak load management can be achieved by gaining insight into energy use across the whole supply chain.
- Manufacturers are beginning to appreciate the need of regulating and monitoring their resources as natural resource costs rise and environmental awareness rises. This is known as green sourcing.
- Water is used for various functions in production, from material cleaning and transportation to sanitation and housekeeping, such as providing drinking water to employees. As a result, companies not only use a lot of water (around 22% of total global use), but they also squander a lot of it, with 80 percent of wastewater released back into the environment without being properly treated. Small but useful adjustments could include training employees on conserving water and even spot problems or placing water metres on the production floor. Another recommendation is to install wastewater management systems or fill machines that are always pushing the boundaries in terms of water efficiency. For example, our third-generation filling machines can now be equipped with water reduction conversion kits to reduce overall use by up to 50%.
- Using more sustainable packaging is a great approach to reduce waste output. Creating all aseptic carton packaging with recyclable materials makes it easy for our consumers to control the carbon impact of every source they use by guaranteeing that our products are sustainable. Another important aspect of waste management is prevention, which includes performing frequent checks on machinery to decrease downtime and finding creative ways to reuse as many by-products as possible. Repurposing by-products, returning excess materials to suppliers, or, at the most basic level, implementing a waste management system that ensures all waste is properly segregated before being disposed of are all examples of this.
Sustainable Factories and Carbon Neutrality
Industries are trying to understand the advantages of transitioning to a carbon-neutral business model. So how can factories that are environmentally friendly lead the way? In today’s connected world, producers have the potential to develop a plethora of new products and learn how to source more ecologically friendly, sustainable materials, adopt digitalisation, make items recyclable and reusable to extend their lives, and decarbonize the energy system.
- By 2050 and 2060, the heavy Industry and heavy-duty transportation sectors in both developed and developing countries can reach net-zero carbon emissions. The industry might significantly impact global CO2 levels if more manufacturers embrace sustainable factory methods, with fossil fuels and Industry accounting for 36.8 billion tonnes of global greenhouse gas emissions in 2019, up 0.6 percent from the previous year.
- Switching from fossil fuels to renewable energy would be a key approach to reduce emissions, with biomass and solar thermal systems helping to revolutionise industrial heating processes. With on-site wind turbines or solar panels allowing industries to capture energy, electrification is another long-term and ecological solution.
Conclusion
Building sustainable factories is the most crucial factor for all production engineers to consider, not because it is a fad, but because it is a requirement and a responsibility to the environment we live in. Environmental responsibility is not only excellent for business, but it is also becoming an intrinsic component of how products are advertised, acquired, and run, according to the most successful manufacturing companies. As a result, it’s critical to think about sustainability at every stage of the manufacturing process.